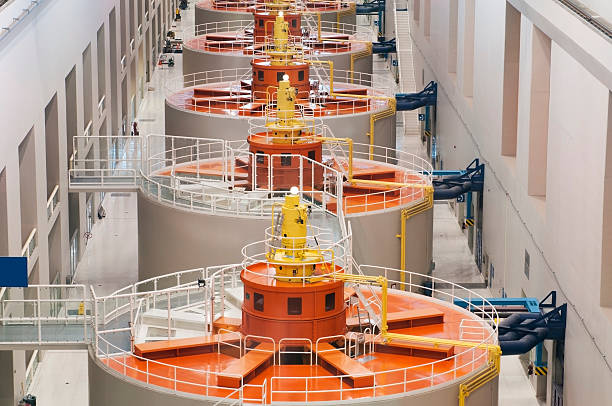
Condition Monitoring
Condition monitoring is the process of monitoring a parameter of the machinery conditions (pressure, temperature, vibration, oil debris, etc.) to identify an abnormal change, which is indicative of a developing fault and predicts the future condition of machines while in operation.
Condition monitoring is a big component of predictive maintenance. The data collected from condition monitoring over time provides valuable information about the current and historical state of an asset. This evolution of a machine can be used to anticipate how the asset will perform over time and how it might degrade, allowing for the scheduling of maintenance based on these predictions. This is known as predictive maintenance – maintenance based on what failures may occur and what maintenance should be scheduled to prevent such failures from occurring.
Implementing (CBMS) maintenance philosophy the level of planned and scheduled corrective maintenance will increase production to over 80% and total maintenance volume and costs will go down 20% to 30%.
Over the years of our experience in the field of condition monitoring technology helped to serve the need of the machinery availability for uninterrupted continuous production. Condition Monitoring through Predictive maintenance would be helpful tool in achieving the above goal.
- The need to predict equipment failures
- The need for a holistic view of equipment conditions.
- The need for greater accuracy in failure prediction.
- The need to reduce the Effect of Maintenance cost.
- The need to improve equipment and component reliability.
- The need to optimize equipment performance.
- Increase in Overall Equipment Efficiency (OEE).
- Increase in Life Cycle Profit (LCP) of the Equipment.
- Reduced maintenance costs.
- Extended the machine availability.
- Total Productive Maintenance (TPM) can be achieved.
- Uninterrupted production is possible.